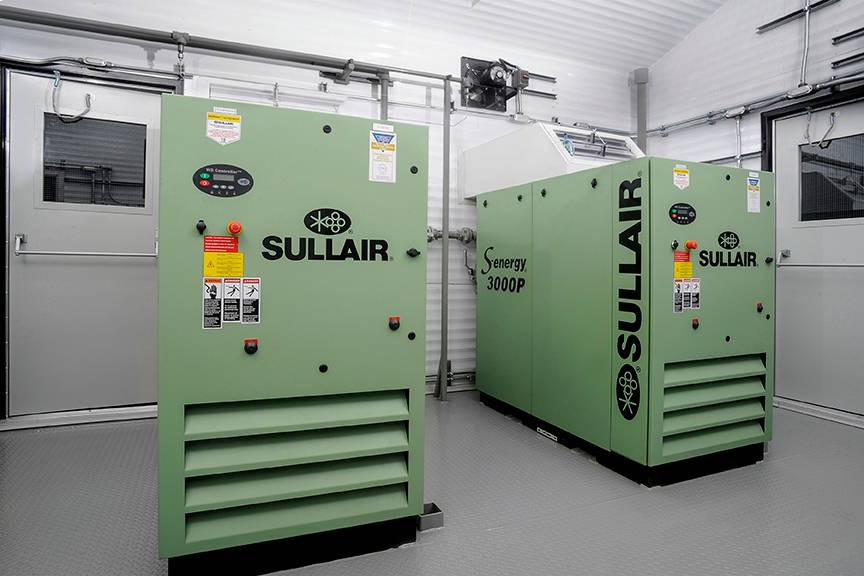
No matter the size of your operation, your industrial compressed air system likely makes up a significant percentage of your total energy usage, which ultimately impacts your overall operating costs. With the cost of energy being so high, it’s only natural that you’d want to improve efficiency to reduce your energy costs. In addition, improving the efficiency of your compressed air system means there’s less energy draw, which will reduce the environmental impact of your operations.
In this guide, we’re sharing the best ways to improve your air compressor energy efficiency, so you can take full advantage of the cost-saving and environmental benefits.
Energy Savings Tips for Your Air Compressor System
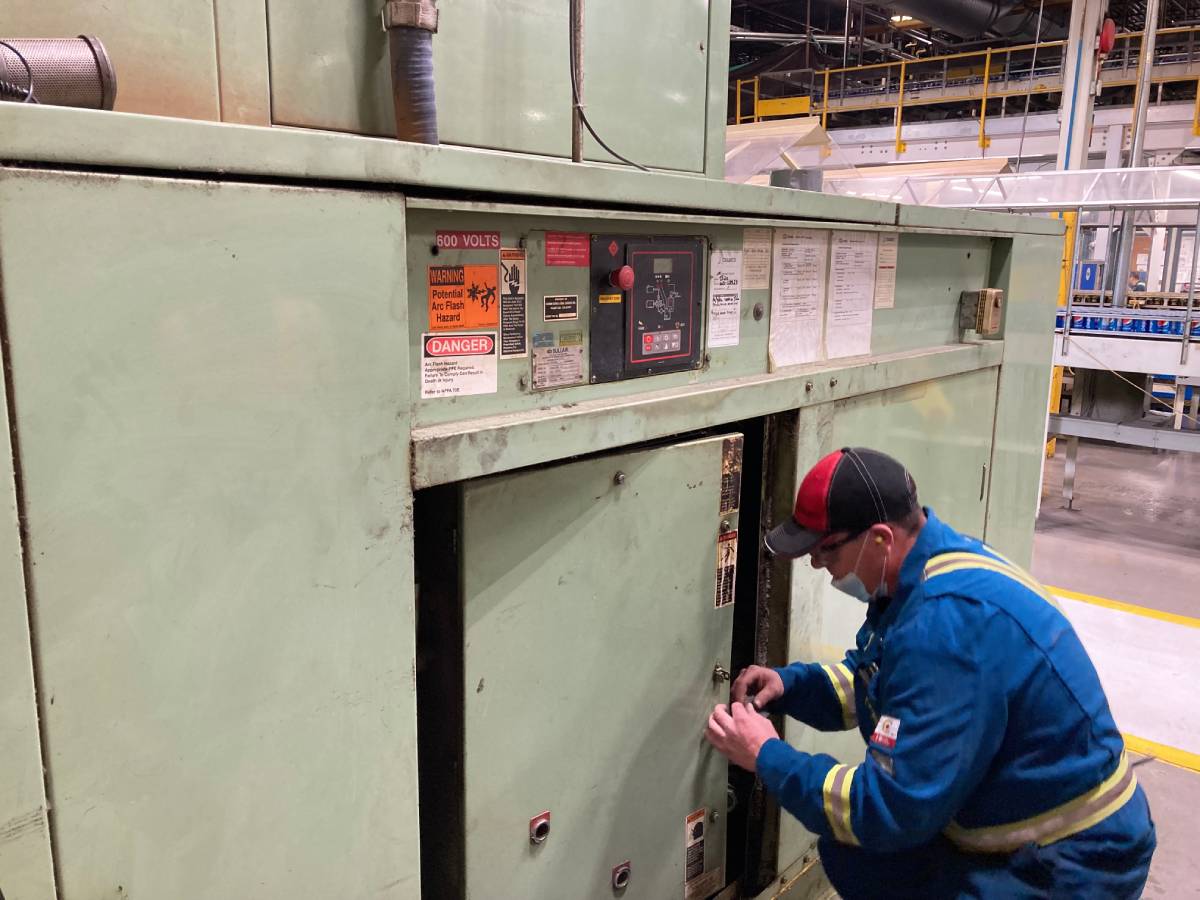
Providing regular air compressor maintenance is essential to ensure maximum compressed air energy efficiency. Without regular maintenance, your compressor will end up wearing out or working harder than it should, which will ultimately reduce its efficiency and lower your energy savings.
As part of your maintenance plan, your authorized supplier should ensure your unit has been properly commissioned, the parameters are properly set and your equipment is functioning optimally.
The overall system design is also an important aspect. Look beyond the compressor itself to see where else you can be more energy efficient with your compressed air systems. For example, examine your piping network to confirm there’s no friction and check whether the style fittings and piping configuration are correct.
It doesn’t always require significant changes to your air compressor systems to make them more energy-efficient. Sometimes, it’s the small changes or additions that can have the biggest impact.
Whether it’s downgrading your system to a smaller compressed air system or making changes to your existing air supply system, there are a number of ways to improve the energy efficiency of your compressed air equipment.
Here are four tips to improve your air compressor energy efficiency.
1. Choose Energy-Efficient Alternatives
To improve energy efficiency in your facility, you may want to consider changing your compressor to a more energy-efficient alternative. You can also make some modifications to your existing unit to improve its energy efficiency.
Spiral Valve Compressors
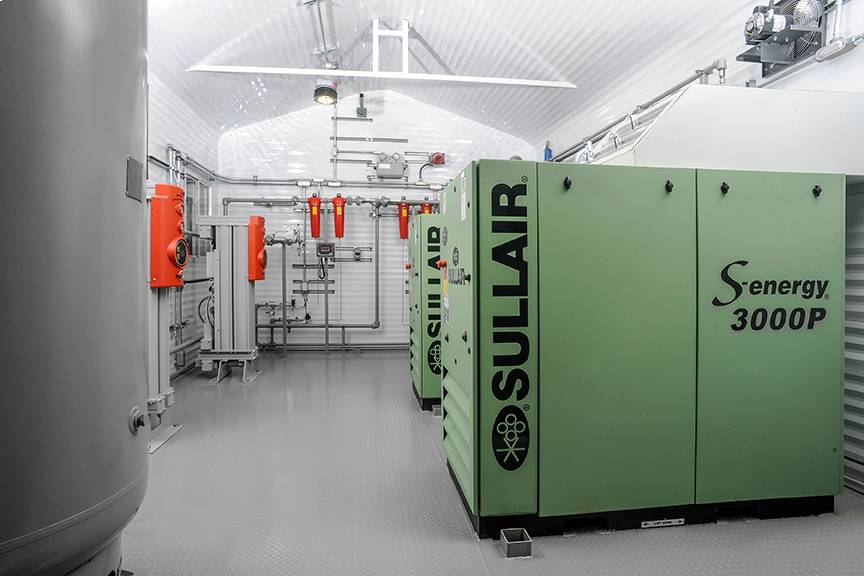
A good option to make your air compressor system more energy efficient is to change to a spiral valve compressor. A spiral valve compressor utilizes the full compression chamber of the air end and reduces energy usage by ensuring that the output matches the system air demand. As air demand is reduced, the spiral valve turns, opening some bypass ports, and reducing the length of the compression chamber.
Sullair’s spiral valve compressors are a cost-effective solution as they have a variable capacity control system to efficiently manage changes in compressor demand. This reduces the amount of air compressed which in turn reduces energy usage and ensures you have a much higher return on your energy costs.
Inlet Modulation
Modulating your air compressor’s inlet control can also improve energy efficiency. Inlet modulation involves throttling the inlet valve, which restricts the amount of air coming into the inlet based on demand. The compressor draws in less air, matching compressor capacity with air usage for steady air pressure control.
VFD Drive
A VFD drive can be applied to a compressor control to regulate and optimize compressor discharge pressure. However, it’s not ideal for very tough environments and may require more maintenance.
2. Downsize Your Compressor
“Bigger is better” is not always the case when it comes to air compressors. Having the right size air compressor for your facility will go a long way towards significant energy savings. Ideally, air compressors should be operating at around 75%. Having a compressor that is too big and running on a much lower percentage may lead to reliability issues and increased energy consumption.
When deciding on which air compressor system is right for your facility, don’t make the decision based on the peak load as it’s unlikely the compressor will be functioning at peak capacity the entire time. There will be periods of peak load, and other times where the system will be operating at a reduced load. A good option is to consider having two smaller compressors that would only need to operate together at full capacity during peak times and then, during lower load times, only one compressor is needed.
3. Find & Resolve Compressed Air Leaks
Even the smallest air leak can significantly affect your air compressor energy efficiency.
On average, with a new air compressor system, around 5% of energy consumption is due to air leaks and an air compressor loses around 1% of its capacity due to air leaks each year.
At Chamco, we’ve seen compressors with air leaks causing up to 60% of the energy consumption. In such cases, before looking to upgrade the system, a simple compressed air audit can determine the air consumption and where leaks may be affecting energy usage and capacity. Instead of upgrading or expanding your compressed air system, when you resolve the air leaks, you can immediately reduce your energy costs and avoid purchasing additional capital equipment.
Air leaks can be detected with specialized ultrasonic video technology. The technology takes a picture of the leak and provides a report on where the leaks are coming from. It also determines how much compressed air and energy are being wasted.
By helping them improve their air compressor energy efficiency, Chamco has helped customers save thousands of dollars in energy costs. Recently, when a customer with three 50HP compressors was looking to add a fourth compressor, we first recommended doing an air audit and leak inspection to determine their actual air consumption. When we adjusted the controls of the existing compressors and fixed a number of leaks, the customer didn’t need to add a compressor and only needed to run one or two compressors with a significantly reduced annual energy cost from $71,000 to $56,000.
4. Change Filters Regularly
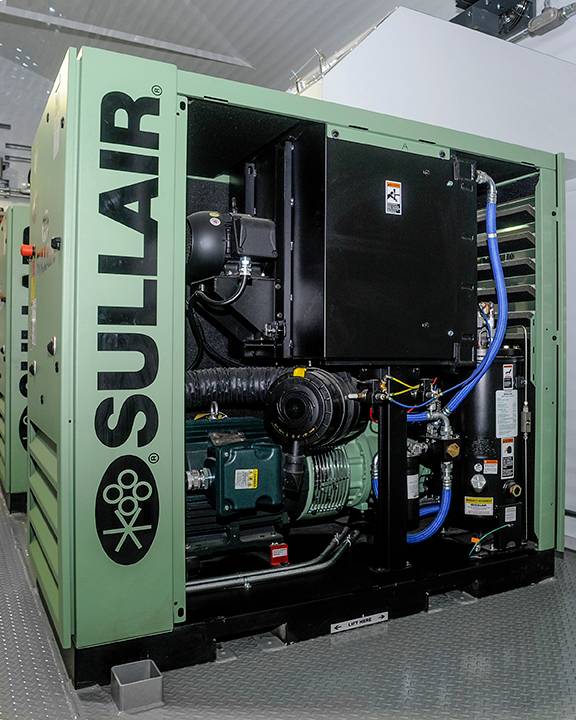
Dirty or clogged air filters can block your air compressor, restricting its ability to pull in and compress air and often leading to overheating. This will ultimately reduce the efficiency of your compressed air system.
Air filters should be changed at least semi-annually or every 4,000 hours (whichever comes first). In extremely dirty environments, such as coal mines, dirty filters will need to be replaced more regularly.
The quality of a filter will also affect your system efficiency. Better quality filters will not need to be replaced as often. When assessing the quality of a filter, examine the guarantee, determine the pressure drop across the filters, and know the supplier’s recommendation on how often they should be replaced.
Let Chamco Help You Reduce the Wasted Energy of Your Compressed Air System
Chamco has the expertise and experience to ensure our customers have the proper compressed air systems in place. We’ll work in partnership with you to maximize your air compressor energy efficiency.
As a starting point, we will conduct a compressed air audit to determine how your system is operating and assess the consumption patterns. From here, our dedicated design and engineering teams will develop a comprehensive strategy to maximize efficiency and compressor performance. We’ll provide simulations of how an air system can be operated and provide different options to consider to improve your air compressor energy efficiency.
Contact us today to discuss the next steps required to ensure the best industrial air compressor energy savings for your business.