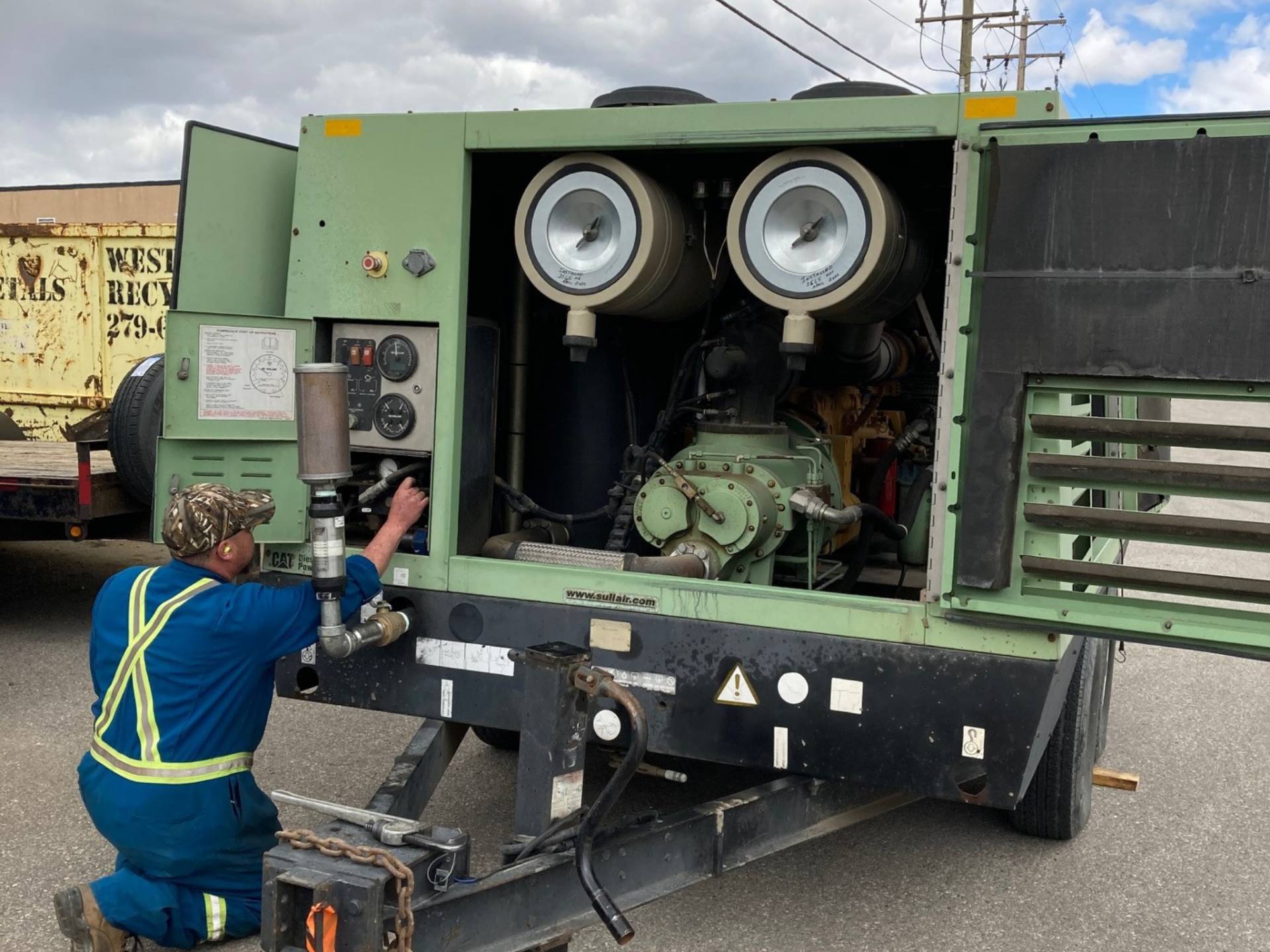
A new industrial air compressor is a significant investment that you would be remiss not to protect through proper maintenance. In this air compressor maintenance guide, we’re giving you all the tips you need to take care of your compressor and extend your air compressor life span, so you can save money and make good use of your investment for years to come.
Why is it Important to Maintain Your Compressor?
Here are a few reasons why it’s so important to invest in regular preventative maintenance for your air compressor rather than waiting for something to go wrong.
Experience a Longer Compressor Lifespan
As we’ve already mentioned, proper maintenance can result in a longer-lasting compressor. In fact, you can generally expect a well-maintained compressor to last around 15-20% longer than a compressor in the same operating conditions that doesn’t receive regular maintenance. This means that although most compressors operating in a good environment can last for over 100,000 hours, compressors that are not maintained well may only operate for as low as 80,000 to 60,000 hours.
Reduce Your Service Costs
When you invest in regular compressor maintenance, you can often expect a fixed maintenance cost. On the other hand, when you’re not investing in regular maintenance, you run the risk of compressor malfunctions and unexpected plant downtime, causing you to pay for emergency repair services. These urgent or after-hours service calls will cost you significantly more money than regular maintenance services.
Air Compressor Maintenance Tips
Use the following air compressor tips to help you keep your compressor operating at its peak performance.
Change Air Filter(s)
Dirty or clogged air filters basically choke the air compressor and restrict the compressor’s ability to pull in and compress air. The equipment still uses the same amount of energy but the output of the compressor is reduced.
The air filter is your first line of defence to protect the air compressor from contamination such as dust, pollen & hydrocarbons in the air, so it’s important to change air filters at least semi-annually or every 4,000 hours (whichever comes first). However, this will depend on the compressor’s operating environment. For example, in dusty environments such as coal mines where there are a lot of contaminants or particles in the air, the air filters will become dirty and clogged more frequently, so they’ll need to be replaced on a more regular basis. In order to determine how frequently your air filter needs to be changed, it’s important to inspect your air filter on a monthly or weekly basis (or even more regularly in particularly dirty environments). Consult your equipment manual to confirm service intervals.
When it’s time to address the heavy build-up of dust and dirt on your air filter, it’s always better to replace the filter rather than clean it. You can’t remove all of the particulate matter by cleaning a filter, and you might damage it, causing something to pass through the filter while the compressor is operating and damage the compressor.
Change the Fluid Filter
The fluid filter is your second line of defence and protects the compressor’s critical components such as the screws/rotors and bearings from contamination or debris. Air filters need to be changed semi-annually or every 2,000 hours (whichever comes first). However, this will depend on the compressor’s operating environment. You should also consult your equipment manual to confirm service intervals.
Change the Fluid/Air Separator
The separator is your last line of defence in protecting the air compressor’s critical components from damage. Allowing a separator to remain in place beyond the recommended service interval can lead to increased pressure drop, decreased compressor fluid life and significant loss to the performance and efficiency of the air compressor. It could also cause an air end failure, which is very costly and can lead to a significant amount of downtime.
The separator element in your compressor should be changed out annually or every 8,000 hours. You’ll want to change the fluid filter and the separator at the same time that you change the oil so that the contaminants don’t get into the new oil.
Change the Oil
The fluid of the compressor is the lifeblood of the compressor and serves three key functions in the compressor’s performance.
- Sealing of the rotors or screws, improving the compression.
- Cooling in the compression chamber.
- Lubricating the bearings and shaft seal.
Using and maintaining a quality fluid in a compressor is the number one factor in the overall performance and extended life of the compressor.
At a minimum, oil should be changed on an annual basis. Although some oil is good for up to 10,000 hours of operation, we recommend changing it yearly along with the separator and filter elements. In addition, we also recommend doing an oil sample every 2,000 hours of operation or during every service to see how the fluid is holding up to the environment and the air compressor usage.
Using the incorrect compressor fluid or not utilizing a proper oil sampling program can lead to varnishing of the fluid within the compressor chamber and significantly decrease the performance and life of your air compressor.
This photo is an example of medium varnished compressor rotors and you can see how this would affect the sealing, cooling and lubrication process during compression.
Clean the Aftercoolers
When it comes to aftercoolers, also known as heat exchangers or radiators, it’s important to ensure they are kept clean. Dirty coolers cannot effectively cool the air and the compressor fluid as part of the compression process, causing the compressor to overheat and shut itself off. Also overheating the compressor fluid reduces the life of the compressor fluid requiring more frequent changes.
Sometimes the compressor can overheat, and before shutting off, it can cause the dryer in the compressed air system to intake hotter and hotter air. When the dryer intakes hot air, it becomes more difficult for the dryer to remove the moisture.
Generally, to prevent the compressor from overheating, it’s important to clean your cooler annually. However, if your compressor operates in a particularly dirty environment such as a sawmill or lumber mill, you may need to clean your cooler monthly, weekly, or even daily. On the other hand, you might get away with cleaning your cooler every few years in a particularly clean environment.
Inspect the Pressure Safety Valve
Pressure safety valves ensure that your air compressor doesn’t create too much air pressure. The inspection of the pressure safety valves is regulated by pressure authorities. For example, in Alberta, it’s the Alberta Boilers Safety Association (ABSA) and in BC, it’s Technical Safety BC (TSBC).
At a minimum, pressure safety valves should be inspected annually, although you might need to inspect them more frequently, depending on the pressure system procedures that you’ve set up with your regulatory authority.
Tighten Screws, Nuts and Bolts
Over time, it’s possible that the fasteners on your air compressor can loosen. Every time air compressors are serviced, whether it’s on a quarterly, semi-annual or annual basis, it’s a good idea to check the screws, nuts, and bolts and tighten any fasteners that have become loose. Remember to check your equipment manual for the tightening procedures and torque requirements.
Compressed Air System Maintenance Tips
Our maintenance tips extend beyond your air compressor! Here are even more tips to help you extend your compressor life span.
Maintain the Entire System
Not only is it important for you to maintain your air compressor, but you also need to maintain all of the different equipment involved in the compressor system in order to get the most out of your compressor.
For example, maintaining your air dryer is important because it is responsible for the quality of the air in your plant and the air used in the compression process. You also need to maintain your receiver or storage tanks because they are responsible for your storage capacity, which impacts whether your plant can run properly.
Check the Drains
As the compressor operates, your wet air tank will fill with condensate. Wet air tanks should be set up with either a time solenoid drain or a zero-loss drain which should continually drain the condensate during the operation of the air compressor. However, in the event of a drain failure, you could risk flooding your tank, sending water down into your plant and causing serious damage to your instrumentation.
For example, a 100 HP air compressor can produce two gallons of water per hour. In humid environments, you can expect to have even more condensate accumulate in your receiver.
We recommend checking your drains daily with the test drain button to ensure there aren’t any issues that could cause catastrophic damage to your plant. At Chamco, as part of our standard protocol, we’ll install a manual check valve before the drain, so you can crack the valve and see if water is building up.
Check for Air Leaks
Due to age or even poorly installed piping, you might experience air leaks in the piping or discharge system connected to your compressor.
Air leaks can be detected with an ultrasonic video system that can identify leaks with the use of ultrasonic pulses. The technology takes a picture of the leak and provides a report on where the leaks are coming from and how much compressed air and energy are wasted as a result.
Regulate the Ambient Temperature
Finally, it’s important to ensure that the ambient temperature surrounding your compressor isn’t too hot or too cold. The ideal room temperature for a compressor is 10 to 20°C, and ambient temperatures outside of this range will force your compressor to work harder. At higher temperatures, you may also have issues with the oil temperature rising, and at lower temperatures, your compressor might freeze.
Bonus Tip: Hire A Pro!
Performing proper maintenance on your compressor and compressed air system requires a lot of skill and technical knowledge. Not only is it a good idea to hire a professional to assist you with your compressor maintenance, but it’s also important to ensure that the technicians providing you with your maintenance services are qualified. You’ll want to ensure that the company you hire has properly trained their technicians and has good quality and safety programs in place to keep you protected.
Extend the Life Of Your Compressor with Chamco’s Preventative Maintenance Program
In summary, if you’re not cleaning your coolers, changing your filters, monitoring your oil and completing the other necessary maintenance tasks on your compressor and system, you could end up paying higher electricity costs and drastically reducing the life span of your equipment.
The amount of time and money you’ll need to spend on compressor maintenance will depend on a few factors, including your environment and compressor usage. For example, an auto body shop that only operates a compressor for eight hours a day, five days a week might get away with semi-annual or even annual maintenance checks. On the other hand, a lumber mill or a coal mine with compressors running 24/7 would need to invest in more regular maintenance to ensure their compressors continue to operate at their best.
At Chamco, our skilled technicians can perform preventative maintenance and inspection checks at a schedule that meets the needs of your compressor. We’re confident that we can limit your downtime with our preventative maintenance programs. If you experience any issues with your compressor outside of your maintenance schedule, we will come down to your site and troubleshoot the problems free of charge.
Additionally, as part of our service plan, we complete a customer care inspection form every time we perform a service on a compressor. Each technician also completes a 100-point checklist to ensure that every checkpoint is addressed and nothing gets missed.
Contact us today to get started with our industry-leading compressor maintenance programs so you can have peace of mind knowing that your air compressor investment is protected.