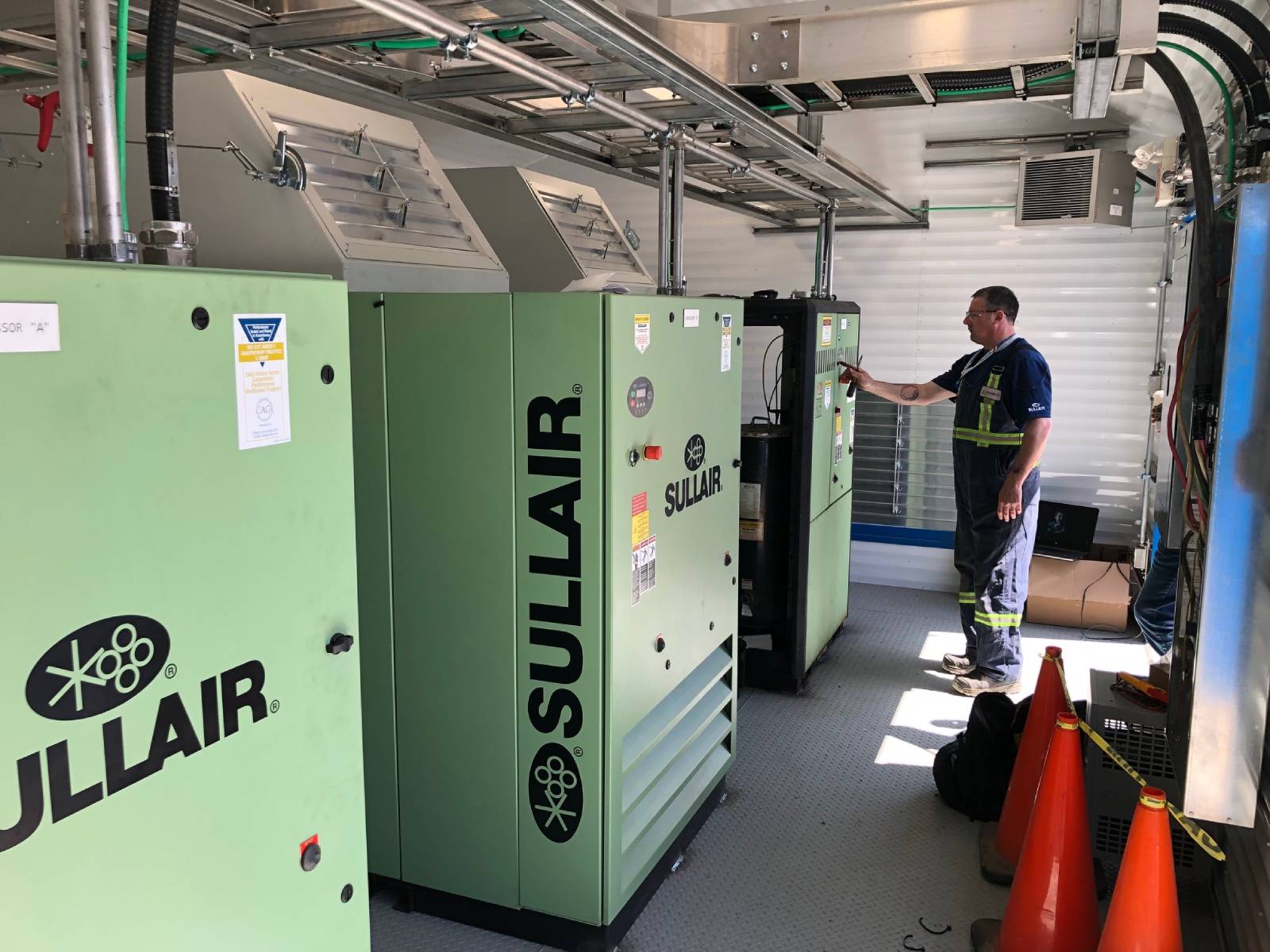
Air compressors are the unsung heroes of industrial applications, powering crucial processes. Yet, these mechanical workhorses are susceptible to various issues impairing their performance and efficiency, leading to expensive repairs and operational disruptions. Ignoring these problems isn’t just a minor oversight; it’s a direct path to operational chaos and costly downtime.
This blog post dives into the frequent problems plaguing air compressors, equipping you with the necessary insight to detect and proactively address these issues. Discover effective strategies for industrial air compressor troubleshooting and maintenance.
1. Air Leaks
Leaks are among the most expensive air compressor problems, yet are often the most overlooked issue.
Leaks in air compressors often stem from a variety of issues, such as worn or damaged seals and gaskets, loose joints in the piping, corrosion of metal parts, faulty or improperly sealed valves, and cracks in hoses or tanks.
Operators often fail to notice leaks in air compressors unless there’s a major compressor failure. Typically, these leaks are identified during routine maintenance or when an unexpected compressor shut-down occurs.
Leaks are regularly overlooked because the operators don’t see the electric bill and the accountants don’t see the compressor operation. So there is no way of reconciling the normal operational costs and the impact of an air leak. A one-time $50 repair can often save $200-$2000 per year on your electrical bill, so it’s important to catch leaks before they become a major liability. It’s also important for the broader green energy efficiency conversation.
An air audit or a leak detection audit, or ideally both, will typically detect an air leak and give you the cost in dollars.
2. Compressor Won’t Start
When an air compressor doesn’t start, it clearly indicates something is amiss. If you press the start button and nothing happens, there could be various reasons why. For instance, even if the controller acknowledges a start request, the compressor might not activate if the system pressure is already above the set start pressure. In this case, the unit will automatically start only when needed.
It’s important to check the current compressed air system pressure. Are there multiple compressors in the system? It’s possible that the inactive compressor isn’t needed because the others are fulfilling the system’s requirements.
If the issue is with the compressor itself preventing it from starting, the problem could lie in the electrical system, or possibly mechanical. For example, the motor might be running, but the compressor remains inactive due to a broken coupling between the compressor and the drive motor.
When troubleshooting a compressor that won’t start, first check the electrical system, ensuring connections are secure and power is supplied. Then, verify if the air pressure is below the compressor’s cut-in setting. It’s a good idea to also inspect the motor-compressor coupling for any breakage or misalignment, check for air leaks, and examine the compressor for any mechanical damage.
If initial troubleshooting doesn’t resolve the issue, it may be time to call a professional service technician.
3. Low Air Pressure
When your air compressor isn’t maintaining pressure, the issue often lies downstream of the compressor. Potential causes include a closed or blocked valve or a malfunction in the dryer causing low pressure in the plant but not being detected by the compressor.
Alternatively, a substantial air leak could deplete more air than the compressor can supply.
Other issues might include misaligned control settings, a faulty valve or sensor, or a broken coupling between the compressor and its drive motor.
To begin troubleshooting, check for visible signs of the above issues, confirm all valves are in their correct open/closed position and operational, and inspect for any leaks in the system. If these checks don’t resolve the issue, professional technical assistance is likely required.
4. Inadequate Cooling / Overheating
Air compressors generate significant heat, and oil is crucial in dissipating this heat. So, if your air compressor is overheating, the first thing to check is the oil levels.
Other things to check include:
- A high ambient temperature
- The heat exchanger
- HVAC issues such as closed dampers or clogged filters
If you’ve checked the oil levels, ambient temperature, and HVAC factors, and these are all satisfactory, then it could be a rarer compressor fault, like a failing thermostat or an internal blockage in the heat exchanger. So you’ll need to check these.
Addressing a failing thermostat is relatively straightforward as long as you have the correct replacement part. On the other hand, resolving a blockage in the heat exchanger is more complex, often requiring the removal of the exchanger for repair.
If the issue is simply a dirty cooler, the cleaning approach will depend on the site conditions. It might be possible to clean the cooler on-site while it’s still installed. Alternatively, it might be necessary to remove the cooler from the unit for cleaning or, in some cases, send it to an external radiator shop for a thorough cleaning.
5. Electrical Problems
The scope of possible electrical issues in compressors is broad, ranging from malfunctioning motor starters, tripped circuit breakers, or blown fuses due to overload. Faulty wiring or loose electrical connections can also lead to operational failures.
Solutions might be as simple as pushing a reset button or replacing an inexpensive fuse, or as costly as replacing an expensive motor.
While an electrician may sometimes be needed, an experienced compressor mechanic usually can identify and perform the necessary repairs. There’s a wide array of potential problems that could be present, and it often requires the expertise of a seasoned compressor technician to spot potential failures and energy inefficiencies before they result in significant damage. Many of these issues are not easily noticed by operators during their routine checks.
6. Oil Carryover / Excessive Oil Consumption
Oil mixing with compressed air instead of staying inside the machine is a significant concern, especially for processes that demand oil-free air.
Some processes also require very dry air, which necessitates a desiccant dryer. However, the desiccant can degrade quickly if it comes into contact with oil. It’s the role of the oil separator to prevent this from happening. If the separator allows too much oil to pass through, the scavenging system might not be able to collect it all, or the system might be clogged and unable to function properly.
You, therefore, need to examine the oil separator and check for any system leaks or malfunctions that could be causing the issue.
Sometimes, the issue may be due to operating conditions that fall outside the machine’s design parameters. Regular maintenance by factory-trained technicians is key to preventing these problems from occurring.
If the oil carryover issue is minor, it can usually become apparent during routine maintenance, like a three-month service check. A technician might notice they’re needing to add more oil than usual. Normally, oil levels in these machines drop only slightly over time. A significant drop indicates oil escaping from the system, which shouldn’t happen.
The critical question, then, is: where is the oil going? For some applications, products cannot be contaminated with oil from the air, requiring extensive filtration to ensure there’s no oil present after the air filter. Therefore, oil loss from the machine can have a direct impact on the effectiveness of downstream filtration.
7. Pressure Fluctuations
Every air compressor system experiences pressure fluctuations. The key questions to consider are: how significant are these fluctuations, and how much control does the compressor have over them? Are we dealing with a single compressor, or is it part of a network of compressors working in unison?
In examining pressure issues, assess the pressure variations both at the compressor and throughout the plant to identify if the issue lies with the compressor control components, communication errors between multiple compressors, or if the system’s demands are beyond the compressor’s control capabilities.
Adjustments to operating parameters might be necessary to match changing air flow demands within the plant. Additionally, it’s important to check if the piping is correctly sized.
In cases where the cause of the issue is not immediately apparent, conducting an air audit can be beneficial. The audit can help in properly sizing a receiver, identifying a compressor that isn’t operating at peak efficiency, or suggesting a more effective control method.
8. Oil Contamination
Clean oil, with the right type and viscosity, is essential for a compressor’s optimal performance. Issues can occur due to various factors such as dirt ingress, the wrong oil viscosity, airborne contaminants like engine exhaust or chemicals in the compressor room, incorrect lubricant, or failure to change the oil at recommended intervals.
It’s crucial to adhere to the manufacturer’s guidelines regarding the appropriate lubricant, as well as the air and oil filters, and their replacement schedule.
Conducting regular oil analysis helps in the early identification of potential problems, allowing for timely interventions to prevent damage.
9. Short Cycling / Excessive Cycling
The frequency at which a compressor switches between “Load” and “Unload” states varies based on several factors, including the size of the compressor, system demand, storage capacity, and capacity control. This timing can range from as short as three minutes to as long as three months.
If you notice a significant change in the timing – for instance, it used to take a long time but now switches in just a few seconds or minutes – it indicates a change in the compressed air system.
A technician can often trace the problem to issues with the operating setpoints, a closed valve, a malfunctioning dryer, or a stuck minimum pressure valve on the compressor sump.
10. Vibration
Vibration in air compressors can be caused by various issues, including misalignment, wear, imbalance, improper foundations, and several other less common factors. It’s crucial to determine if there are unacceptable vibration levels and to diagnose the underlying cause.
The solution could be as simple as tightening a mounting bolt, or it might require a major overhaul of the compressor unit or motor.
Implementing a vibration monitoring program is essential for identifying these issues early on, allowing for planned interventions to prevent unexpected failures.
Regarding installation factors such as misalignment and improper foundations, these issues often originate from how the air compressor is set up. However, they can also develop over time. For example, an improper foundation might cause a broken weld under the frame, leaving the machine unsupported.
Deterioration can occur either due to installation errors or long-term use, making regular checks and maintenance crucial.
11. Pressure Relief Valve Activation
The Pressure Relief Valve (PRV) is a critical safety component in an air compressor system. When it activates, it usually indicates a malfunction in another part of the system, often because the compressor didn’t unload correctly.
The primary suspects in such a case include the pressure sensor, unload solenoid, inlet valve, and blowdown valve. The PRV’s function is to prevent the system pressure from exceeding the safe working limit.
Addressing a PRV activation involves thorough testing to determine the cause of the pressure increase. It’s possible that the issue isn’t with the system pressure exceeding the PRV’s set limit, but rather that the PRV itself has weakened over time and is now activating at a lower, normal pressure range. Determining the actual cause of failure is essential.
12. Corrosion and Rust
Rust and corrosion occur when the components of an air compressor come into contact with water, and there is excessive moisture in the system. This moisture can cause various complications and impact the functioning of the compressor.
In some cases, the cause could be straightforward, like exposure to rain or snow due to environmental conditions at the site. More commonly, however, it’s the humidity in the air that leads to rust and corrosion.
Ideally, the aim is for the humidity in the air to pass through the compressor’s sump as vapour. It should then condense in the cooler and be eliminated at the water separator. If water condenses in the sump, it usually indicates that the unit isn’t operating at a sufficiently high temperature.
It’s crucial to identify the source of the excess moisture. Once the origin is pinpointed, it becomes possible to tackle the fundamental issue, thereby preventing corrosion and other related problems in the system.
13. Excessive Noise
Compressors typically aren’t quiet machines. However, changes in their sound can offer important clues that something may be wrong. Learning from experience is key to understanding their normal sounds and recognizing changes.
Loose components and general wear and tear can cause excessive noise in an air compressor. To troubleshoot noise issues, conduct a thorough inspection of the compressor, checking for loose components or signs of wear and tear.
Regular maintenance, such as lubricating moving parts and replacing worn-out elements, can often resolve noise issues. If you cannot identify the cause of the sound change just by listening, vibration analysis can be a useful tool in diagnosing the problem.
How Chamco Can Help With Your Industrial Air Compressor Troubleshooting
Chamco has the necessary expertise and experience to ensure you have the most effective compressed air system. We will collaborate closely with you to diagnose and solve any air compressor issues, ensuring your systems are running optimally and reliably.
Our team, consisting of factory-trained technicians based in six locations throughout Western Canada, is dedicated to delivering tailored support to match the specific needs of your compressor.
We offer a broad range of services, including OEM parts supply, round-the-clock phone and onsite technical support, and preventative maintenance programs, to ensure you have total peace of mind when it comes to the operation and performance of your industrial air compressor.
Contact us today to discuss your industrial air compressor needs.