CASE STUDY
How Chamco Helped The Climax Mine Project Build State-Of-The-Art Mining Facilities with a Large Pump System

Project Background
The Climax Mine in Climax, Colorado, United States is one of the oldest mines in the U.S. For many years, the mine was the largest molybdenum mine in the world and produced 75% of the world’s supply of the metal, which is commonly used in steel and other metal alloys to increase strength and durability.
After the Climax Mine’s first shipment in 1915, the mine was shut down and re-opened a few times. In 2012, the mine reopened again after a 17-year shutdown. To get the Climax mine ready for re-opening, the owners started a major reconstruction project to build state-of-the-art mining facilities. As part of the project, Chamco was tasked with supplying a large pump system to work in conjunction with an upgraded water treatment facility on the mine tailings pond.
The Challenge
Chamco was responsible for all aspects of this unique project, from design to on-site start-up of the pump system. The Climax Mine Project presented 3 key challenges: system, size, location.
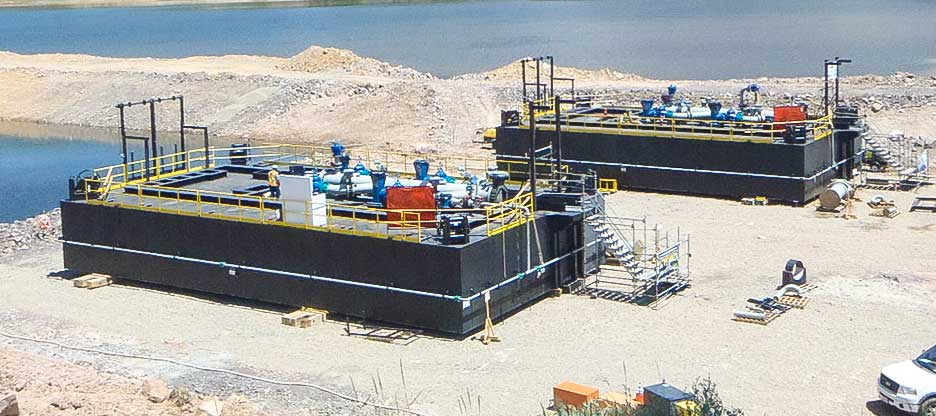
The Solution
The Climax Mine pump system installation presented many engineering, logistical, environmental and site-specific challenges for Chamco. We successfully overcame each one of them and proudly delivered a unique installation to meet our client’s requirements.
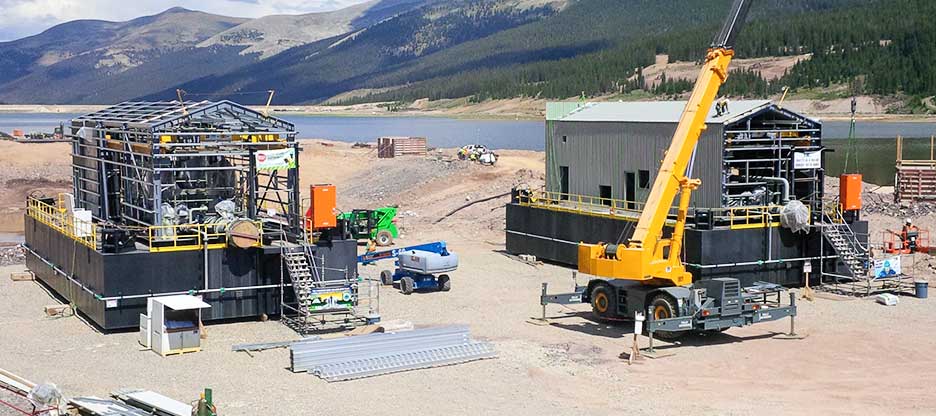
The Results
Both pump systems were successfully started in 2012 and have been a reliable asset for the Climax Mine ever since!

Learn more about how Chamco can help with your project.